In recent years, there has been a growing need for carbon fiber steel plastics as a lightweight, elastic composite with excellent mechanical properties to replace heavy steel and aluminum in various industries such as aerospace, automotive, energy, construction, and sporting goods. Until now, carbon fiber has been limited to special high-end products such as motor sports, sports cars, and luxury yachts due to its high unit cost. However, with the recent advancement of manufacturing processes and the expansion of the market, the manufacturing cost of carbon fiber reinforced plastics (CFRP) has reached an affordable level and has been widely applied in various major industries.[Carbon Fibre Reinforced Plastic (CFRP) Composites Market Report 2017-2027]
First of all, in the automotive sector, lightweighting is a long-standing technical discipline. In recent years, fuel economy and emission regulations in developed countries have made lightweighting a necessity for automakers and parts manufacturers, and it has emerged as a matter of survival for the automotive industry. As evidenced by recent events such as Volkswagen’s (VW) emissions cheating and fuel economy manipulation by several major OEMs, which have caused major problems worldwide, it is technically very difficult to meet the increased environmental standards by improving the performance or efficiency of internal combustion engines alone, and it is known that it is currently reaching its limits. In particular, in the future, the weight of automobiles will increase as consumers demand more safety and convenience features in their cars, and as a result, the lightweighting of automobile bodies is increasingly recognized as an important key technology to meet automobile fuel economy requirements and emission regulations.
With the recent tightening of automobile fuel economy and emission regulations in developed countries, the interest of automakers and parts manufacturers in lightweighting technologies has never been higher. In particular, lightweight body structure technology using lightweight metals and composites is considered to be the most realistic and powerful way to meet current environmental regulations.
In particular, major overseas automakers are focusing on the development of lightweight automotive parts and bodies using thermosetting/thermoplastic carbon fiber composite materials (CFRP) to meet environmental regulations and consumer demands. This is because, for example, a 100 kg reduction in vehicle weight can save 0.3 to 0.5 liters of fuel per 100 km of driving distance, and CO2 emissions can be reduced by 8.0 to 12.5 g/km. In particular, electric vehicles (EVs), hybrid electric vehicles (HEVs), and plug-in hybrid vehicles (PHEVs), which are expected to become a new paradigm in the automotive market, are also expected to see an increase in the application of CFRP to reduce vehicle weight due to high-capacity batteries. Until now, CFRP has mainly been applied to interior and exterior parts such as roofs, hoods, and trunk lids, which are non-structural parts of automobiles. When looking at the weight reduction effect of applying CFRP, only very limited lightweight effects can be achieved, such as 6.0 kg reduction in the roof and 8.0 kg reduction in the hood. Therefore, it is essential to apply lightweight metals or CFRP to the body structure in order to reduce vehicle weight by more than 100 kg to meet environmental regulations. A representative example is BMW’s i3/i8, which achieved a dramatic weight reduction of ~120 kg compared to steel by applying a body-in-white (BIW) skeleton of CFRP to the i3 model.
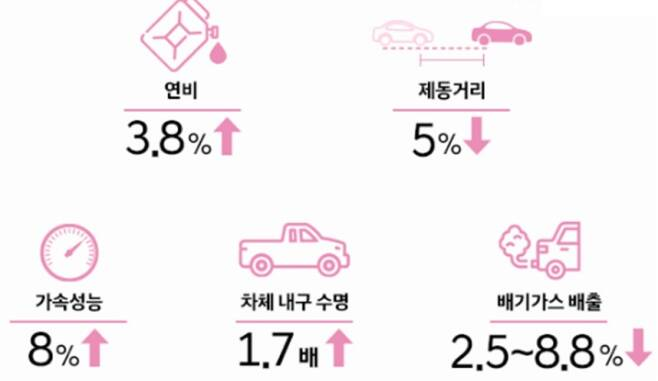
In the aerospace field, fiber reinforced plastic (FRP) materials have been developed since the 1940s and were first applied to the B-36 bomber in 1949. In particular, CFRP (Carbon FRP) materials have been used for fuselage structure design in the military and aerospace sectors, such as space shuttles and stealth warplanes, and have been applied to civilian applications since 1980. It is a new material that is attracting attention in the aerospace industry and construction field because it is very light, corrosion-free, and has a tensile strength and stability of 5 to 10 times that of iron.
Since the 1980s, CFRP has been considered for application to tail wings, the airframe structure of aircraft, and has been adopted in Airbus A310, 300, 320, and Boeing B77. In recent years, CFRP main wings have been adopted for the F-2 military aircraft and Boeing’s B787, and the proportion of CFRP used has expanded from 10 to 20 percent to more than 50 percent.
It is also the first airliner to fully utilize the B787-900-S- CFRP< aircraft. By increasing the percentage of CFRP in the aircraft to 50%, the fuel efficiency was improved by 20% through lightweighting without sacrificing rigidity, and 30 additional seats could be installed.
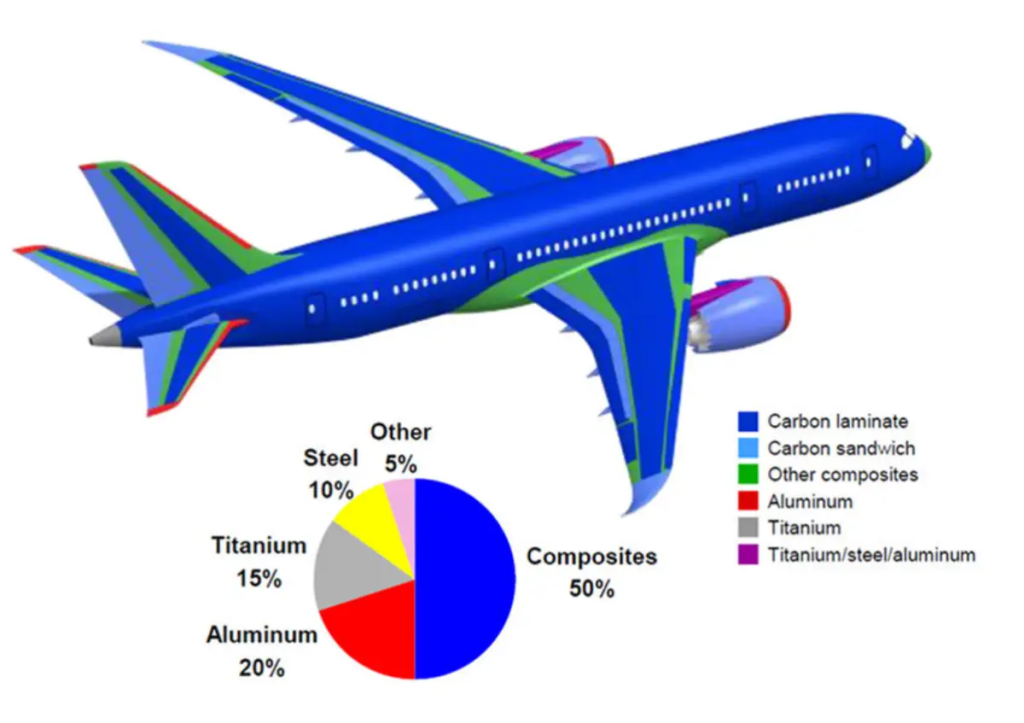
In addition to the ever-expanding application of CFRP in the aerospace and automotive industries, the application of CFRP in the marine, offshore, rail vehicle, and sports industries is expected to continue to increase, and the development of cost-effective and productive molding manufacturing processes must be made in line with this.