The idea of combining two or more materials to create a material with enhanced mechanical properties not available in a single material is not a new concept. The history of composites can be traced back to the production of air-dried bricks used in the construction of the pyramids in ancient Egypt, where the bricks were made with straw to increase the strength of the bricks in response to the problem of brittleness when using only earth and stone. Traces of this composite material can also be found in Korean earthen walls. Our ancestors also used rice straw mixed with mud to make solid earth walls.
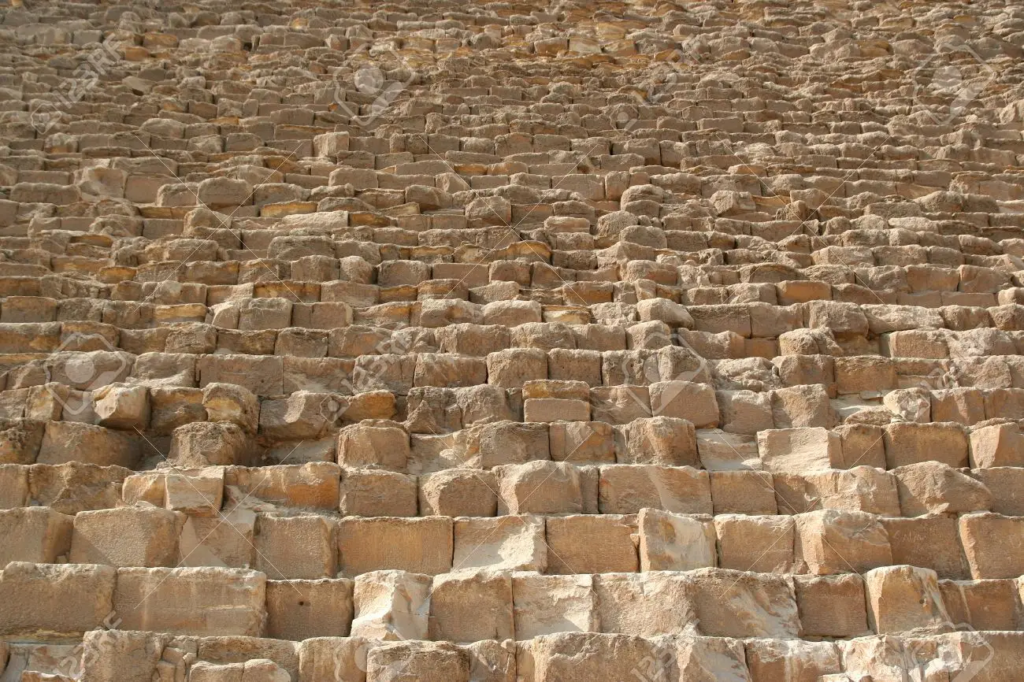
The birth of modern composites is said to have been marked by the manufacture of tires using fiber-reinforced rubber (1888), or by the manufacture of glass fiber reinforced polyester (1942). The latter can be considered the first, as it mainly utilizes the strength of the fiber. From this point on, research and development of lightweight, high-strength (high specific strength) structural materials began.
The modulus of a typical glass fiber is as small as 70 Gpa, and numerous research and development efforts have led to the development of several types of fibers. This research and development was a key part of the U.S. Apollo program, which spurred the development of composite materials. Boron fiber (383 Gpa modulus) was developed through this process. In the early 1970s, carbon fiber finally appeared in a sophisticated way.
With the development of various high-performance fibers, it has been recognized that fiber-steel composites are not just alternative structural materials, but materials that maintain mechanical properties in extreme environments that were not possible until now, and research on improving the matrix to maximize the use environment has progressed rapidly. In terms of polymer resins, the choice has expanded from polyester to epoxy, polyamides with high heat resistance, and thermoplastics with good mass production. For high-temperature applications, metals and ceramics are also being considered as base materials. In addition, the development of fibers for steel materials has also progressed rapidly, with functionalized carbon fibers, silicon carbide fibers, and amide fibers suitable for base materials. As these fibers have become highly functional, the development of base materials to maximize their properties has also progressed rapidly, bringing about synergistic effects and expanding the diversification of composite materials.
The first generation of composites, Glass Fiber Reinforced Plastics (GFRP), which were initially lightweight and high-strength; second-generation composites, such as Carbon Fiber Reinforced Plastics (CFRP) and Boron Fiber Reinforced Plastics (BFRP), are more advanced, high-strength materials; and third-generation composites, such as Metal Matrix Composites (MMC) or Fiber Reinforced Metals (FRM), are heat-resistant materials, Ceramic Matrix Composites (CMC), which are heat resistant materials.
So what is the fourth generation of composites? Perhaps one is hybrid composites. An example is the combination of aramid-based composites and carbon fiber composites, where the materials compensate for the weaknesses of the compressive strength properties of aramid fibers and the damping properties of carbon fibers. Another is functional composites. So far, composites have only considered mechanical properties, but functional composites are materials that consider thermal, electrical, and electromagnetic functions.